
In most instances, I use my CAD/CAM program to insert the Macros, ie M03 and MO2, and other M commands. Any help there, other than having to redraw it in TurboCAD? As you know, it then does not select them to be machined, when creating the toolpath. I've tried to use the select open, declare as boundry function, but it does not turn the selection to red, as the other closed boundries are. dxf drawing with TurboCAD, now it seems the lines did not connect, for I get a green line on importing it to DeskCNC, ie an open boundry.
#DESKCNC KEY CODE ISO#
What is the difference between selecting Post Processor ISO G-Code or ISO Post Processor Non-Modal? I'm currently using Non-Modal.
#DESKCNC KEY CODE SOFTWARE#
How do I get the DeskCNC software to automatically insert an M03 command in the beginning of the created g-code file? I now have to edit the file in Notepad, insert the M03 just before the tool plunges, insert the M05 after the last tool raise, and remove the automatically inserted M02 and M05 from the end.Ĭan I edit the code directly from a DeskCNC page, or must the code be edited with another application. Now that the card is working, I've discovered other areas of "attention". I have an E-stop switch installed in my housing, I'm about to wire that up today. The only connections I have, is the 12V supply, the 3 axis step and directions, and the Ouput I/O CW, to a solid state relay. I have not wired anything to the Input I/O connector. My jog and contour speeds are fine, it takes a day and a half to plunge the 5mm down into the workpiece.Ī last question, what is your latest version software and firmware? If the startup screen shows the firmware as 2.24, is that what is loaded into the controller, or is that what is in the software? Does one have to manually force the controller to update, to get the latest version of firmware loaded into the controller? Where do I set the tool plunge speed, mine takes ages to plunge into the work surface.
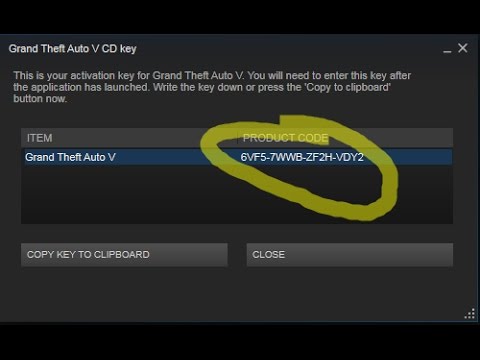
Thanks for your help, it gave me hope to at least sit in front of the PC, and figure it all out. dnc file as before, I had it saved in a different location, and low and behold, the thing worked !! Afterwards, I went and checked every seingle set-up page, all are exactly the same values, selections, names, ALL THE SAME as before, but now it works !!
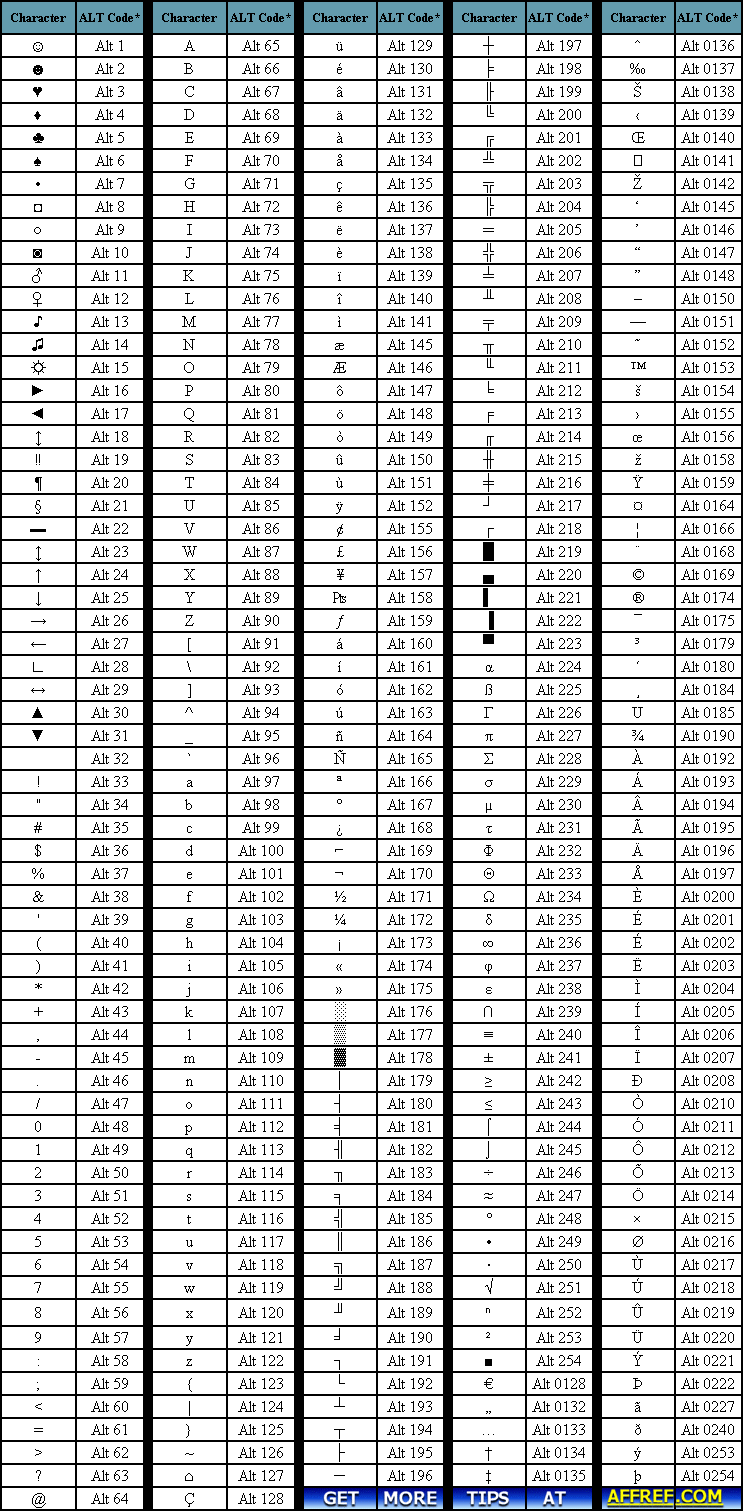
I set up the Machine Axis and Steps/mm only, as well as Disabled the E-stop Terminal. When checking the version, once installed, it showed up as version 2.0.1.108, Firmware 2.24. I wiped the DeskCNC directory from my PC, and installed the file DeskCNC v2_0_1_99.Exe all over again. I did what goes against my logic, and that was to uninstall it all. Please check if you can find anything wrong. When the cut starts as a straight line, it will cut to the first change of direction, then hit this invisible limit. The error happens when going from line 10 to line 11.ĭoes the same with other files, right after lowering the z-axis, or when hitting the first corner, it hits a limit switch.
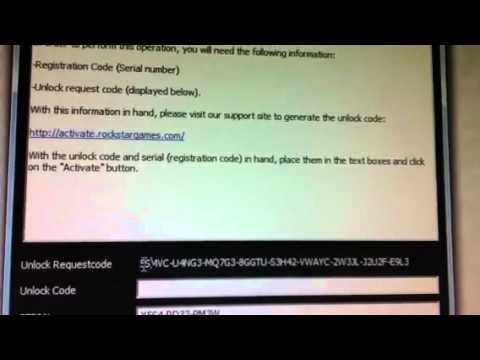
I have attached my CAD file, as well as the cut file. The message on the bottom left says "Limit Switch Hit". I hit Go, it starts up, jogs the router to the first entry, lowers the Z-Axis, but when it has to start cutting, it hits some or other Limit, stops the program execution. I cancel the E-Stop by hitting Reset, all the controls now active.
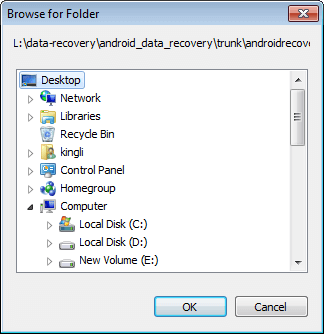
dnc, it goes to Machine Mode, I confirm the file is loaded, I can see the G-code in the bottom. dxf file with DeskCNC, go to Select All, go to Toolpath, select Contour, enter 2 as the Contour Depth, hit Contour, back to Toolpath, select Run Machine, save the file as a. When I open the DeskCNC application, I can jog all 3 my axis, no hassles. I'm trying to cut an extremely simple part.
